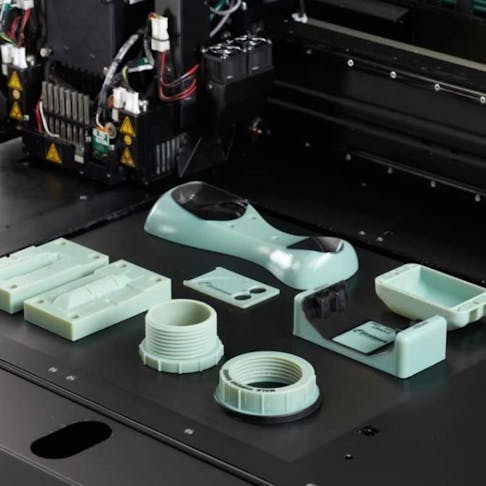
Material Jetting 3D Printers: Definition, Process, Components, and Materials
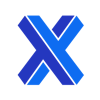
Material jetting (MJ) 3D printers represent a cutting-edge additive manufacturing process that creates objects by depositing material layer by layer. Similar to inkjet printing, MJ printers use a printhead to dispense droplets of a photosensitive material, which then solidify under ultraviolet (UV) light. This process allows for the creation of parts with high dimensional accuracy and a smooth surface finish.
The printhead, build platform, material container, and UV-light source are important parts of MJ printers. A vast variety of materials are suitable for use, such as: acrylics, thermoset photopolymers, and casting waxes. We will examine the intricacies of its operation, the variety of its uses, and more as we go further into the realm of material jetting 3D printers.
What Is Material Jetting?
Material jetting (MJ) is an additive manufacturing process that operates similarly to 2D inkjet printing. In MJ, a printhead dispenses droplets of a photosensitive material that builds a part layer by layer. This part is then solidified under ultraviolet (UV) light.
How Does the Process of Material Jetting in a 3D Printer Work?
The process involves several steps:
- The liquid resin is heated to achieve optimal viscosity for printing.
- The printhead travels over the build platform, depositing tiny droplets of photopolymer to the desired locations.
- A UV light source is attached to the printhead. This light source cures the deposited material. It creates the first layer of the part by solidifying it.
- The build platform then moves downwards. This process is repeated until part completion.
What Are the Different Components of Material Jetting in a 3D Printer?
The main components include:
- Printheads: Dispense the material onto the build platform.
- UV-Light Sources: Cure and solidify the deposited material.
- Build Platform: Where the part is constructed layer by layer.
- Material Container: Holds the liquid resin before it is jetted.
What Are the Different Materials That Can Be Material Jetted in a 3D Printer?
Material jetting in 3D printing is versatile, accommodating a range of materials, each with unique properties and applications. Here's an explanation of various materials used in material jetting:
1. Ceramics
Ceramics in material jetting are advanced due to their high temperature and wear resistance. The process involves jetting ceramic particles suspended in a photopolymer, which is then cured layer by layer with UV light. Post-processing includes the removal of the polymer matrix and sintering to enhance strength. This process is suitable for intricate geometries that are unattainable in standard ceramic manufacturing, which is why the aerospace, medical, and electronics industries find it ideal. The final products have outstanding chemical and thermal stability, which is often required under challenging conditions.
To learn more, see our full guide on Ceramics.
2. Metals
Material jetting for metals involves jetting fine droplets of a metal-infused binder onto a build platform. After deposition, these droplets are solidified through thermal or UV curing. The parts then undergo a debinding process to remove the binder, followed by sintering to fuse the metal particles. This technique allows for the creation of metal parts with intricate details and complex geometries that would be challenging to produce with traditional manufacturing methods. It's particularly useful for producing small, detailed components with a smooth surface finish in industries like jewelry and dental supplies, and in manufacturing prototypes.
3. Plastics
The plastics used in material jetting are photopolymers, which harden when exposed to ultraviolet light. The method is to create each layer of the desired object by putting tiny droplets of photopolymer onto a build platform. This process is renowned for its extreme precision and capacity to create objects with intricate details and flawless surfaces. Prototyping, consumer items, and dental and medical models are among its many applications. A wide range of mechanical qualities, from hard to flexible, are also possible with the diversity of photopolymers that are currently accessible, meeting the needs of a wide range of applications.
4. Composites
Composite materials in material jetting are created by combining two or more distinct materials to harness their combined properties. Typically, this involves embedding fibers or particles into a photopolymer matrix, which is then jetted and cured layer by layer. The result is a part that benefits from the strength and stiffness of the fibers while maintaining the versatility and design freedom of the matrix material. This technology is particularly beneficial for applications requiring parts with enhanced mechanical properties, such as in the automotive and aerospace sectors.
To learn more, see our full guide on Composites.
5. Waxes
The main purpose of waxes in material jetting is to create intricate patterns for mold-making and investment casting. The method is spraying melted and solidified materials that resemble wax to create the part's layers. The clean burnout characteristics of these materials are what make them ideal for molding without residue. In the jewelry and dental sectors, in which accuracy and attention to detail are critical, this application is essential. Traditional wax carving processes take a lot longer and cost a lot more money, but the material jetting can create complicated wax patterns quickly.
6. Resins
Resins, particularly photopolymers, are a cornerstone of material jetting. These liquid materials are jetted onto a build platform and cured using UV light, forming solid objects with high accuracy and smooth surface finishes. Resins offer a range of properties, including transparency, flexibility, and high-temperature resistance, making them suitable for a wide array of applications from prototyping to end-use parts in industries like: automotive, consumer products, and healthcare.
To learn more, see our Best Resin for 3D Printing guide.
7. Silicones
Silicone materials are becoming more and more common in material jetting because of their heat resistance, flexibility, and biocompatibility. To create a solid elastomeric component, jetting silicone entails depositing droplets of a silicone prepolymer and curing them. The medical industry benefits greatly from this technology for creating custom prostheses and organ models due to silicone's similarity to human tissue in terms of feel and mechanical properties.
To learn more, see our guide on What is Silicone.
8. Bioinks
Bioinks are specialized materials designed for 3D printing tissues and organs. They consist of a biocompatible matrix, often a hydrogel, that supports cell growth and differentiation. In material jetting, bioinks are jetted and solidified to create scaffolds that mimic the extracellular matrix, providing a conducive environment for cells to form functional tissues. This technology holds promise for regenerative medicine, drug testing, and understanding disease mechanisms. The challenge lies in optimizing the material properties to ensure cell viability and function post-printing.
9. Photopolymers
Material jetting uses photopolymers because of their fast solidification under UV light. To create exact and intricate pieces, these liquid resins are injected into tiny droplets and then cured layer by layer. Photopolymers are adaptable and can be used for a wide range of applications, from end-use part manufacturing to prototyping, thanks to their ability to be manufactured with different qualities including: rigidity, transparency, and color. They are perfect for intricate components, consumer items, and dentistry applications due to their high resolution and flawless surface finish.
10. Support Materials
Support materials in material jetting are essential for creating overhangs and complex geometries. They are often jetted simultaneously with the build material and act as scaffolding during the printing process. These materials are designed to be easily removed post-printing, either by dissolution in a specific solvent or by manual removal. The ability to use support materials expands the design possibilities in material jetting, allowing for the creation of parts with intricate internal structures and moving components.
Each of these materials brings unique properties and advantages to the table, enabling the creation of parts that meet specific requirements for a wide range of applications. Material jetting continues to evolve, pushing the boundaries of what can be achieved in additive manufacturing.
How To Choose Material for Material Jetting 3D Printers?
When selecting a material for material jetting 3D printers, consider the following factors:
- Final Part Requirements: Determine the mechanical, thermal, and aesthetic properties needed.
- Material Properties: Assess the compatibility of material properties with your part's requirements.
- Cost: Factor in the material cost and its impact on the overall project budget.
- Availability: Ensure the chosen material is readily available and compatible with your printer.
- Post-Processing: Consider the ease of post-processing and the desired finish of the final part.
What Is Material Jetting?
In 3D printing, material jetting is a precise procedure that involves spraying tiny droplets of photosensitive material onto a build platform to construct objects. The UV light cures these droplets instantly, hardening them to create every layer of the part and producing intricate geometries with excellent resolution.
To learn more, see our guide on What is Material Jetting.
Is Material Jetting Necessary in 3D Printing?
No, material jetting is not necessary for all 3D printing applications. It is one of several technologies available, chosen for specific use cases whenever its advantages align with project requirements.
What Is the Advantage of Material Jetting 3D Printers?
The advantages of material jetting 3D printers include:
- High Precision: Capable of producing parts with intricate details and complex geometries.
- Excellent Surface Finish: Parts have a smooth finish, often comparable to injection molding.
- Material Variety: Compatible with a wide range of materials, including multi-material and full-color printing.
- Speed: Unlike FDM printers, material jetting printers can print multiple parts simultaneously without loss of speed.
- No Post-Curing: Materials are fully cured during the printing process.
What Is the Disadvantage of Material Jetting 3D Printers?
The disadvantages of material jetting 3D printers include:
- Cost: Generally more expensive than other 3D printing technologies.
- Material Limitations: Not all materials can be used, and some may degrade over time.
- Build Size: Typically limited to smaller parts due to the nature of the technology.
- Mechanical Properties: Parts may have poorer mechanical properties compared to those made with technologies like FDM or SLS.
- Maintenance: Printers may require more maintenance due to the complexity of the technology.
What Is the Difference Between Material Jetting and Binder Jetting?
Material jetting builds components layer by layer by depositing droplets of photosensitive resin that are cured by UV light. On the other hand, binder jetting entails adding a binder to a powder bed to fuse the powder particles into a component. High precision and surface finish are hallmarks of material jetting, while bigger components and cost-effectiveness are binder jetting’s main advantages.
To learn more, see our guide on Binder Jetting vs. Material Jetting.
Summary
This article presented material jetting 3D printers, explained them, and discussed their different components and materials that can be used. To learn more about material jetting 3D printers, contact a Xometry representative.
Xometry provides a wide range of manufacturing capabilities, including 3D printing and other value-added services for all of your prototyping and production needs. Visit our website to learn more or to request a free, no-obligation quote.
Disclaimer
The content appearing on this webpage is for informational purposes only. Xometry makes no representation or warranty of any kind, be it expressed or implied, as to the accuracy, completeness, or validity of the information. Any performance parameters, geometric tolerances, specific design features, quality and types of materials, or processes should not be inferred to represent what will be delivered by third-party suppliers or manufacturers through Xometry’s network. Buyers seeking quotes for parts are responsible for defining the specific requirements for those parts. Please refer to our terms and conditions for more information.
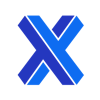