Custom Die Cutting Services by Xometry
Upload your CAD files to get an instant quote for die cut parts. No minimums. Get parts in days and free standard shipping on all US orders.
Xometry offers the highest quality custom die cutting services, catering to the diverse needs of different industries and businesses. We are proud to be ISO 9001:2015 and AS9100D certified, which ensures that we adhere to industry best practices.
Die cutting is a versatile manufacturing process that involves cutting various materials into precise shapes using specialized dies. With a wide range of processes and materials available, Xometry's custom die cutting services deliver exceptional precision and efficiency.
What Is Die Cutting?
Die cutting is a manufacturing process used to cut out precise shapes from materials such as paper, cardboard, fabric, leather, foam, plastic, and various other materials. It involves the use of a specialized tool called a die, which is a sharp-edged blade or a set of blades formed into the desired shape. The die is mounted onto a press, and the material to be cut is placed underneath it. When the press is activated, it applies pressure to the die, causing it to cut through the material and create the desired shape. The die can be custom-made to produce specific shapes, such as letters, numbers, logos, or intricate designs.
In addition to cutting, die cutting can also perform scoring, perforating, embossing, or debossing. Scoring creates creases or fold lines in the material; perforating creates small holes or dotted lines; embossing raises the surface to create a raised design; and debossing creates a depressed, or indented, design. Die cutting methods are most effective for high-volume, repetitive production runs due to the significant initial investment needed to acquire the die.
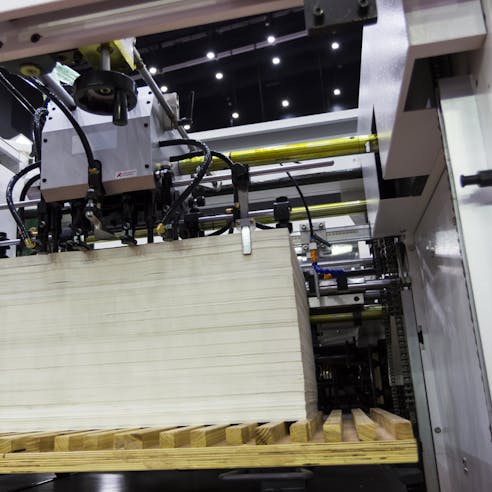
Types of Die Cutting Processes
- Rotary Die Cutting
- Flat Bed Die Cutting
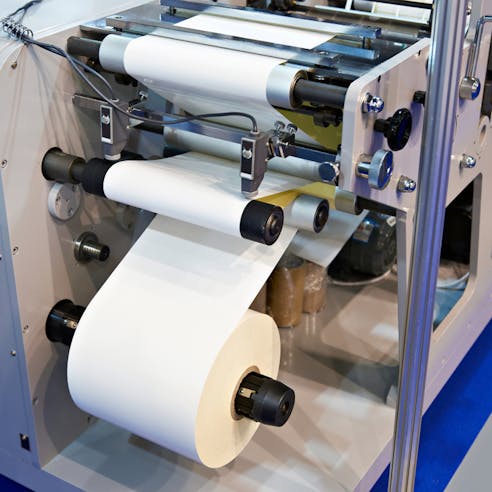
Rotary Die Cutting
In rotary die cutting, the material is passed between a cylindrical die and an anvil roll. The die is cylindrical and rotates at a high speed, while the anvil roll provides support. This process allows for quick and efficient cutting of materials, as an entire sheet or web of raw materials can be fed into the press at once. Once the machine is loaded, it can cut various shapes and designs with ease. Rotary die cutting services are often used for high-speed production of labels, stickers, and intricate designs.
Flat Bed Die Cutting
The most common die cutting process is known as flatbed die cutting or steel rule die cutting. This process involves the use of a flatbed die cutting press and steel dies to accurately cut raw materials into custom shapes and designs. It is especially effective for cutting thicker materials (more than ⅛ inch in thickness), thanks to its ability to apply significant pressure. The pressure capabilities of flatbed die cutters can vary depending on the specific machine and its design. For example, some flatbed die cutters may have pressure capabilities ranging from a few tons (e.g., 2-5 tons) up to larger machines capable of exerting 20 tons or more. These higher-capacity machines are often used in industrial settings for cutting heavy-duty materials or for high-volume production. Flatbed die cutting is highly advantageous for short production runs, as it can operate in semi-batch or batch production modes. It is versatile and suitable for cutting a variety of materials, including paper, cardboard, foam, fabric, and plastics.
Die Cutting Materials
The suitability of a material for die cutting depends on factors such as its thickness, density, and flexibility. Different materials offer specific advantages depending on the intended application, and die cutting enables efficient and precise fabrication of custom shapes from these materials. There is a wide range of materials that are considered suitable for die cutting, some of which are discussed below:
- Plastic and Plastic Films
- Foam
- Thin Metal Sheets
- Rubber
- Fiber
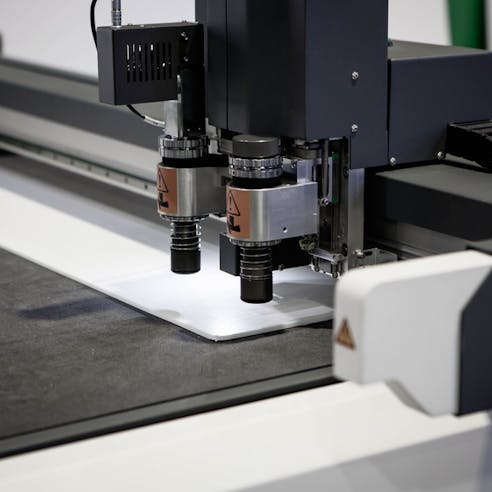
Plastic and Plastic Films
Die cutting services are frequently used for cutting plastic materials such as PVC (polyvinyl chloride), PET (polyethylene terephthalate), polyethylene, and polycarbonate. These materials are widely used in packaging, labels, displays, and protective films. Plastic materials are lightweight, durable, and offer excellent chemical resistance. They can be cut into complex shapes, making them suitable for a wide range of applications. Die cutting allows the precise shaping of plastic materials, making custom shapes and designs possible. Additionally, plastic films often possess adhesive properties, allowing them to be easily applied to surfaces. Plastic films are used for applications like adhesive tapes, window films, and packaging wraps.
Foam
Foam materials like polyurethane (PU) foam and ethylene-vinyl acetate (EVA) foam are commonly die cut. Foam is used in industries such as: automotive, packaging, electronics, and upholstery. Foam materials provide cushioning, impact absorption, and insulation properties. Die cutting foam enables precise shaping, ensuring a snug fit and optimal performance in various applications. The die-cut foam allows for the creation of gaskets, seals, cushioning pads, insulation, and foam inserts for packaging.
Thin Metal Sheets
Die cutting is also utilized for cutting thin metal sheets, typically aluminum, stainless steel, or brass. Thin metal sheets are commonly used in electronics, automotive parts, appliances, and nameplates. Thin die-cut metal parts offer excellent strength, conductivity, and corrosion resistance of metals, but in a lightweight form. Die cutting enables high precision, allowing the creation of detailed metal components and decorative features. Die cutting allows for the precise cutting of intricate shapes, perforations, and embossed designs on metal sheets.
Rubber
Rubber materials such as: neoprene, silicone, natural rubber, and synthetic rubber can be die cut. Rubber is used in applications such as: gaskets, seals, O-rings, vibration-dampening components, and automotive parts. Die cutting provides precise shaping of rubber materials, ensuring a tight seal.
Fiber
Fibrous materials like paper, cardboard, felt, and textiles can be die cut. These materials find applications in packaging, stationery, crafts, clothing production, where the textile has to be cut into a pattern, and automotive interior components. Fiber materials are versatile, lightweight, and easily customizable. Die cutting provides clean and accurate cuts, allowing for intricate designs and precise fitting, as well as allowing the creation of a variety of shapes, patterns, and designs.
In need of custom die cut parts?
Die Cutting Advantages
Die cutting offers several advantages, making it a popular manufacturing process in many industries. Here are some key advantages of die cutting:
- Affordability
- Customizable
- Flexibility and Versatility
- Precision and Accuracy
- Automation and Integration
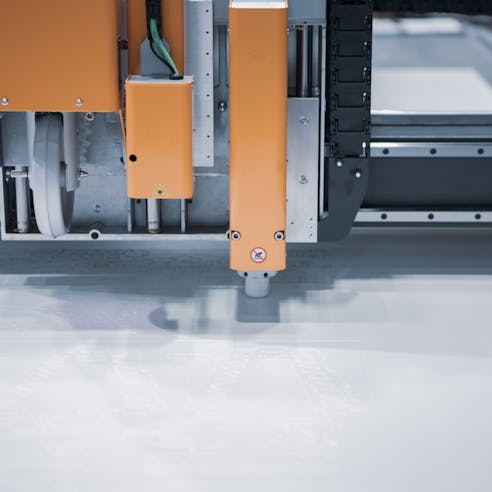
Affordability
Die cutting offers cost advantages, particularly for large-scale production runs. Once the die is created, the cost per piece decreases as the production volume increases. Dies have a long lifespan and can be used for a significant number of cycles, making die cutting a cost-effective solution for mass production.
Customizable
Die cutting allows for high levels of customization. Custom dies can be created to produce unique shapes, sizes, and designs according to specific requirements. This customization capability enables companies to create products that align with their brand identity or meet specific customer needs.
Flexibility and Versatility
Die cutting offers flexibility in terms of material selection. It can be applied to a wide range of materials, including paper, cardboard, fabric, foam, plastics, rubber, and metals. This versatility allows manufacturers to choose the most suitable material for their product's requirements, whether it's for flexibility, strength, durability, or aesthetic appeal. Die cutting allows for the creation of intricate shapes, complex designs, perforations, scoring, and embossing. It can be tailored to suit specific applications and requirements.
Precision and Accuracy
Die cutting provides high precision and accuracy in cutting materials. The use of specialized dies ensures consistent and repeatable results, making it ideal for producing identical shapes and components. This precision allows for tight tolerances and ensures the proper fit and function of the die-cut pieces.
Automation and Integration
Die cutting can be integrated into automated manufacturing systems, streamlining the production process. Automated die cutting systems can increase production speed, improve efficiency, and enhance overall productivity.
Die Cutting Disadvantages
While die cutting has some obvious advantages, it also has some limitations, including:
- May Not Work With Thick Material
- Scoring
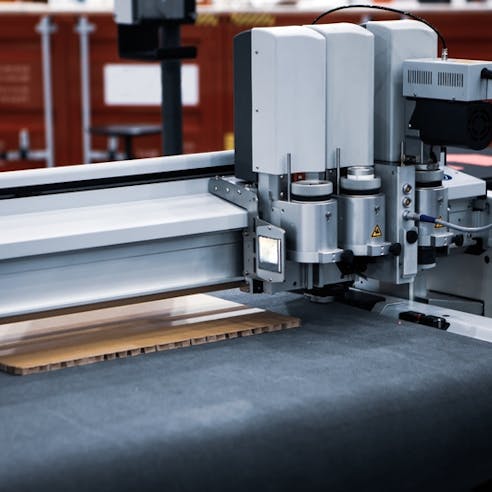
May Not Work With Thick Material
Die cutting is most effective for materials that are relatively thin and flexible. Thicker materials, such as thick cardboard or metal sheets, may pose challenges in achieving clean and precise cuts. The thickness of the material can make it difficult for the die to penetrate and cut all the way through the material, resulting in uneven or incomplete cuts.
The maximum thickness of material that a die cutter can handle depends on several factors, including the specific machine model, its design, and the type of material being cut. While die cutters are generally capable of cutting a range of materials, including thicker ones, there are limitations to consider.
Most flatbed die cutters are designed to handle materials of moderate thickness, such as paper, cardboard, thin plastics, and fabrics. These machines can typically handle material thicknesses ranging from a few millimeters to around 6-10 millimeters, depending on the specific model. The maximum thickness that can be effectively cut will depend on the machine's cutting force, the type of cutting tool being used, and the machine's overall design and capabilities.
In general, if you're working with materials thicker than what a standard flatbed die cutter can handle, you may need to consider alternative cutting methods specifically designed for thicker materials.
Scoring
Scoring is a technique used in die cutting to create indentations or creases in the material without fully cutting through it. While scoring can be useful for creating fold lines or perforations, it has its limitations. Score lines may not always produce consistent results, especially with certain materials. In some cases, scoring may cause undesired tearing or inconsistent folding.
Industries That Use Die Cutting
Listed below are some industries that make extensive use of die cutting, along with examples of applications within each industry:
- Aerospace
- Defense
- Dental
- Energy
- Film
- Mechanical
- Medical
- Packaging
- Public Infrastructure
- Recreation
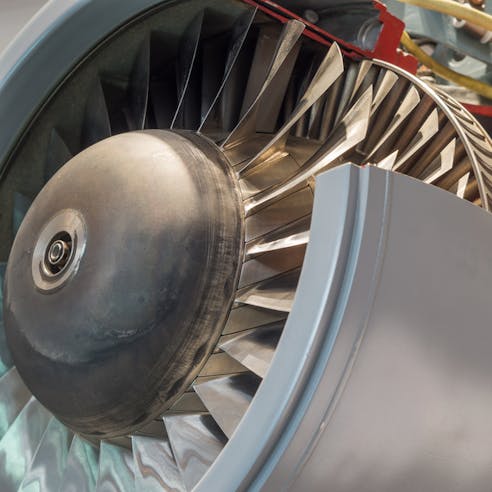
Aerospace
Die cutting is used in the aerospace industry for applications such as gaskets, seals, insulation, vibration-dampening components, and interior trim. Die-cut materials like foam, rubber, and specialty films are utilized to meet the stringent requirements of the aerospace sector.
Defense
The defense industry uses die cutting for applications including gaskets, seals, shock absorption components, insulation, and protective materials. Die-cut products are used in military vehicles, aircraft, naval vessels, and various defense equipment.
Dental
In the dental industry, die cutting is employed for producing products like dental aligners, mouthguards, dental dam materials, packaging, and various dental accessories. Die cutting ensures precise shaping and efficient production of dental materials.
Energy
Die cutting finds applications in the energy industry for gaskets, seals, insulating materials, vibration-dampening components, and specialty films. These products are used in energy generation systems, electrical equipment, renewable energy installations, and power transmission components.
Film
Die cutting film is used for creating intricate designs, logos, and decorative elements used for packaging, labels, displays, and promotional materials. They are also utilized in window films, adhesive tapes, and protective films.
Mechanical
The mechanical industry employs die cutting for applications such as: gaskets, seals, thermal and acoustic insulation, vibration-dampening components, and packaging. Die-cut materials like rubber, foam, and specialty films are used in machinery, equipment, automotive components, and industrial products.
Medical
Die cutting is widely used in the medical industry for manufacturing medical device components, wound dressings, surgical drapes, filters, gaskets, and seals. Die-cut materials like medical-grade foams, adhesives, films, and fabrics are utilized to meet the specific requirements of medical applications.
Packaging
Die cutting plays a vital role in the packaging industry for producing boxes, cartons, labels, inserts, display stands, and various packaging components. Die cutting allows for precise shaping, scoring, and perforating of packaging materials to enhance functionality and visual appeal.
Public Infrastructure
Die cutting is utilized in public infrastructure projects for applications such as: gaskets, seals, insulation, noise reduction materials, and protective components. Die-cut materials are used in bridges, tunnels, railways, roads, buildings, and other infrastructure projects.
Recreation
Die cutting finds applications in the recreation industry for producing products like sporting goods, toys, puzzles, games, and crafts. Die-cut materials like foam, felt, paper, and fabrics are used to create custom shapes and designs for recreational products.
Alternatives to Die Cutting
While die cutting is a widely used manufacturing process, there are alternative methods available for achieving similar outcomes here at Xometry. Here are some alternatives to die cutting:
- Laser Cutting
- CNC (Computer Numerical Control) Routing or Milling
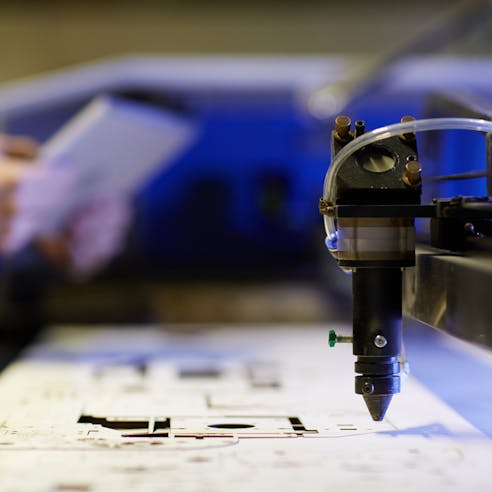
- Laser Cutting: Laser cutting utilizes a laser beam to precisely cut through materials. It offers high precision, intricate detailing, and the ability to cut a wide range of materials, including plastics, wood, acrylics, fabrics, and metals. Laser cutting is particularly suitable for thin and delicate materials or designs that require high levels of complexity.
- CNC (Computer Numerical Control) Routing or Milling: CNC routing and milling involve the use of a computer-controlled machine with cutting tools to carve, shape, and cut materials. It is suitable for materials like wood, plastics, foams, and nonferrous metals. CNC routing offers high precision, versatility, and the ability to create complex 2D and 3D shapes.
Why Choose Xometry for Your Die Cutting Services?
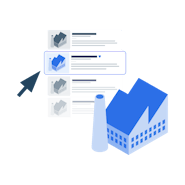
Endless Options
Choose from millions of possible combinations of materials, finishes, tolerances, markings, and certifications for your order.
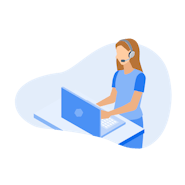
Easy to Use
Get started with our easy-to-use platform and let our experts take care of managing the project from locating the right manufacturing partner to delivery logistics.
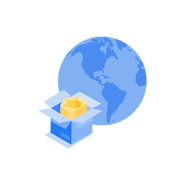
Vetted Network
We are ISO 9001:2015, ISO 13485, and AS9100D certified. Only the top shops that apply to become Suppliers make it through our qualification process.