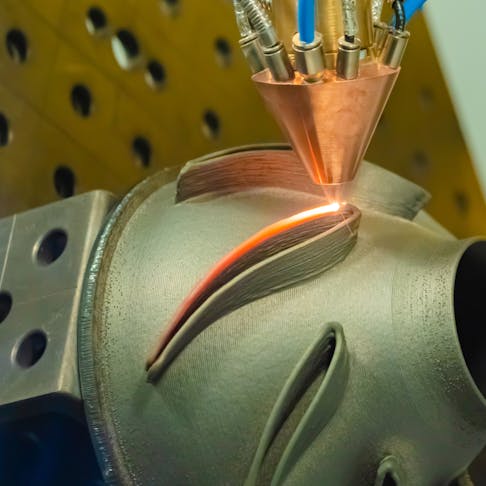
8 Possible Futures of 3D Printing
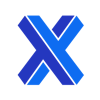
Several exciting prospects are on the horizon for 3D printing developments. Researchers are continually exploring novel materials and processing methods for 3D printing. 3D printing is increasingly being integrated with other sunrise technologies: artificial intelligence (AI), robotics, and virtual reality (VR). These convergences deliver increasingly effective automated manufacturing processes, rapid design optimization, and more-informative prototyping experiences. This family of technologies is central to the development and refinement of Industry 4.0.
The adoption of the more advanced and more accessible forms of 3D printing continues, growing across diverse fields. As the technology becomes more accessible and versatile, its applications will expand into more productization and human-endeavor areas.
This article will delve into eight possible futures of 3D printing.
1. 3D Printed Homes
3D-printed homes represent a nearly groundbreaking innovation in construction, offering a promising solution to rapid and digital building. This is performed by large-footprint 3D printers operating in a concrete material version of fused filament fabrication (FFF), delivering rapid and low-labor construction.
In principle, 3D-printed homes will become more affordable than conventionally built homes, as technology advances. The reduced labor requirement lowers construction costs, making it an attractive option for: affordable housing initiatives, standardized and flexibly customized buildings, and rapid-response construction in disaster areas.
Digitally manufactured homes also have the potential to be more sustainable. The minimization of waste and the use of eco-friendly construction materials, even using primarily recycled materials, can greatly reduce the environmental impact of construction.
2. Construction Industry
Beyond abodes, 3D printing holds immense potential for innovation in the construction industry across a much wider spectrum of applications.
3D printing can be expected, eventually, to fabricate infrastructure such as: bridges, tunnel linings, and dams. Architects and designers can leverage 3D printing to create intricate and customized architectural features, including: facades, ornamentation, and sculptures. The loss of obvious artistry in construction is noted, as cost-saving has defined these features as luxury. 3D printing is likely to free designers from some of these style restrictions.
3D printing enables the fabrication of modular building components, in an off-site kits-set manufacturing process. On-site assembly allows streamlining of the manufacturer/construction process, improving precision and quality control. 3D printing can be used to create urban-facility components such as: benches, planters, streetlights, decorative paving, and retaining walls. Customized features enhance public spaces and improve the aesthetic and functional design of human environments.
The same techniques in development now are likely to become keystones in the longer term in the commercial exploitation of the lunar surface in mineral and Helium-3 extraction.
3. Metal 3D Printing
Research is burgeoning in the range of metal alloys that can be 3D printed. Efforts are being made to optimize existing metal powders for specific applications and to reduce costs and handling difficulties/hazards. The refining of process parameters and optimization of printing conditions deliver higher precision, improved surface quality, and greater dimensional accuracy. This is partly driven by enhancements and step-changes in laser and electron beam technology, and more esoteric advances in powder bed fusion and directed energy deposition techniques. Steady improvements in the speed and productivity of metal 3D printing processes include the development of faster core technologies like multi-laser systems and high-speed powder deposition processes. Less glamorous but equally important are improvements in build chamber design and heat management to reduce print times, improve energy consumption, and increase productivity.
Metal 3D printing is increasingly being adopted for increased volume and part sizes in the production of complex parts and components such as combustion chambers. Evolving equipment and techniques are increasing reliability in large-scale manufacturing operations. NASA, DARPA, and military field maintenance are all driving these developments at a high and increasing pace. Post-processing is a critical aspect of metal 3D printing, and advancements in integration with surface finish, heat treatment, and precision machining of 3D-printed metal parts are necessarily and rapidly developing. This serves to simplify workflows and deliver more finished components with less handling, simpler logistics, and better repeatability.
4. Manufacturing Sector
3D printing will play an increasingly crucial role in advancing sustainability initiatives within the manufacturing sector. More efficient use of materials and support of circular economy principles are expected to result from 3D printing technology penetration into general manufacturing.
Metal 3D printing is in increasingly widespread adoption across the most demanding manufacturing sectors. With developing maturity and improving cost-effectiveness, manufacturers will inevitably adopt it more widely. Developments in 3D printing are enabling the printing of multiple materials within a single build process. This can be expected to increase steadily. This allows for hands-free fabrication of increasingly complex parts and finished products with graded materials/properties.
3D printing continues to be central to Industry 4.0 development. This facilitates automated process monitoring, real-time QC, and automated workflows in manufacturing operations. Developments in material science are resulting in the introduction of new materials for 3D printing: polymers, metals, ceramics, and composites of these and reinforcers. These materials allow the fabrication of parts for a broader range of applications.
3D printing technology is increasingly enabling the decentralization of manufacturing through on-demand production and distributed manufacturing. It will become increasingly practical for companies to be able to produce parts closer to the point of use, for lower operational overheads.
5. Material Innovations
Material innovations in the 3D printing sector are driving significant advances in scope, applicability, and cost, ramping up the capabilities of additive manufacturing technology.
R&D focused on developing advanced polymer materials with enhanced mechanical properties, chemical resistance, and thermal stability is ongoing and accelerating. More commonly printed by FDM®, improving powder bed methods are allowing a wider variety of outcomes/applications and higher resolutions, approaching molded-part properties. Innovations in metal additive manufacturing materials are resulting in new metal alloys with improved strength, durability, and corrosion resistance. The nature of 3D printing is unlike melt processing, so it allows graded alloys (transitioning between metals through a build) and high-entropy alloys (HEAs, percentage fixtures that cannot form a solution in melt processing) to be used.
Ceramic and composite materials are playing an increasing role in 3D printing, thanks to advancements in material science and processing techniques. This holds out the potential for unique properties such as: high-temperature resistance, extreme durability/toughness, anisotropic electrical insulation/conduction, and biocompatibility. In bioprinting, researchers are developing bioinks and biomaterials, direct-cellular printing, and growth framework approaches capable of replicating patient-native tissues and organs. Personalized medical implants, tissue-engineered constructs, replicated organs, and drug delivery systems are all likely near-term developments.
Future material innovations are going to include smart and functional materials with embedded sensors, actuators, and responsive properties typified in 4D printing. This enables the fabrication of smart devices, wearable electronics, and intrinsically functional prototypes.
6. Aerospace Applications
3D printing in the aviation, drone, and orbital sectors is on the cusp of significant growth and innovation.
3D printing localizes and simplifies the fabrication of otherwise impractically complex, lightweight structural components with optimized geometries. These can help reduce weight without sacrificing resilience for improved fuel efficiency. The technologies are revolutionizing the production of engine components such as: turbine blades, fuel nozzles, and combustion chambers. The creation of otherwise non-manufacturable internal features enhances performance significantly.
3D printing technologies are being used to produce components for satellites, spacecraft, and launch vehicles. Orbital manufacture (i.e., outside the Earth’s atmosphere) on-demand will reduce the need for launches — a key need in expected longer-duration missions. Aerospace and military companies achieve greater supply-chain resilience by enabling localized production of highly advanced spare parts and components, minimizing potential supply-chain disruptions.
7. Organ Engineering
Developments in direct and indirect organ engineering via 3D printing approaches offer immense promise for regenerative medicine.
Research into developing bioinks and biomaterials that mimic the extracellular matrix (ECM, scaffold materials) of human tissues is advancing. These create an implantable environment for patient cell growth and differentiation, enabling the population of the scaffold with patient-functional tissues. Bioprinting techniques allow for the deposition of living cells in three-dimensional matrices to create functional tissue structures. The complex architecture and functionality of native tissues and organs are beginning to be developed. This is a rapidly expanding research area.
A major challenge in bioprinting is the incorporation of vascular networks to sustain printed tissues. Researchers are developing strategies to bioprint intermediary structures to promote angiogenesis and vascularization. Research into this is early but promising and liable to develop rapidly.
Bioprinting is merging with microfluidics to create organ-on-a-chip as miniaturized models of human organs for drug testing and disease modeling. These offer the prospect of better predictive models for drug development and personalized medicine. This shortens the time-to-market burden of drug development. The bioprinting of entire functional organs (hearts, kidneys, livers, lungs) for transplantation is in the experimental stage. Significant progress in creating organoids and tissue constructs is happening among academic networks.
As bioprinting technologies proliferate, efforts toward regulatory approval for bioprinted products are progressing in sync. A few bioprinted products have already received regulatory clearance for clinical trials.
8. Advancements in Healthcare
Predicted and envisioned advances in healthcare from 3D printing populate a spectrum of applications that will have transformative effects on patient care, medical procedures, and biomedical research.
Patient-specific implants and prostheses made by 3D printing provide custom-designed aids and orthotics tuned to an individual patient’s anatomy. This perfects fit, enhances function and comfort, and leads to better treatment outcomes and quality of life. Surgeons are increasingly using 3D-printed anatomical models, derived from CAT-scan data to visualize patient anatomy and plan complex procedures. These unique models improve planning/learning, enhance accuracy, reduce surgery time, and generally improve patient outcomes.
Bioprinting technology is beginning to allow the fabrication of functional tissues and organs using patient-derived living cells. These can aid in drug screening, disease modeling, and regenerative medicine applications. 3D printing serves in the fabrication of drug delivery systems, such as: personalized medication doses, controlled-release formulations, and implantable drug-eluting devices. Point-of-care manufacturing of medical devices, instruments, and equipment can reduce reliance on centralized manufacturing facilities and supply chains.
Advances in 3D bioprinting technology are driving research in regenerative medicine, such as: engineered functional tissues, organoids, and bioactive scaffolds for tissue repair and patient cell colonization to treat degenerative diseases, traumatic injuries, and congenital defects. Dental and maxillofacial applications are already in wide use and expanding in capability and market penetration. Fabricating dental prostheses, orthodontic appliances, and surgical guides is commonplace and growing in capability rapidly.
To learn more, see our article on Advancement in Healthcare.
What Is 3D Printing?
3D printing originated as the precise reproduction of 3D digital files in solid materials. It generates slices of the model, through specialized CAM software, creating representations of a finite-thickness slice of the model to be reproduced. Those slices are then reproduced in various materials and by various technologies and machine classes. These are built sequentially to create a stack of slices that are coupled together to make a 3D object.
What Types of Materials Are Being Experimented With in 3D Printing?
Some types of materials being experimented with in 3D printing are:
- Advanced polymer materials such as: PEEK (polyetheretherketone), PEKK (polyetherketoneketone), ULTEM® (polyetherimide) and PPSU (polyphenylsulfone).
- Metal matrix composites (MMCs) such as: ceramic fibers/powders, graphene, or carbon fibers for elevated strength, stiffness and wear resistance.
- Functional materials such as: conductive inks, electrostrictive and electroactive polymers, diamagnetic and paramagnetic materials, or self-healing polymers.
- Nanoparticles, nanotubes, and nanofibers that offer unique properties such as: enhanced strength, conductivity, and thermal stability. Their incorporation into 3D printing formulations results in advanced nanocomposites with various planned and unexpected benefits.
To learn more, see our full guide on Types of 3D Printing Materials.
How Is 3D Printing Contributing to Advancements in Healthcare?
3D printing is beginning to make significant contributions to advancements in healthcare across most medical specializations. Some of these contributions include:
- Allows medical professionals to create highly accurate and patient-specific anatomical models. These are readily printed, based on medical imaging data such as CAT- or MRI-scan data and ultrasound images. These new capabilities assist in preoperative planning, surgical simulation, and patient education. They deliver improved patient and surgical outcomes and reduced operating times.
- Allow the production of customized medical devices, implants, and prostheses tailored to individual patient anatomy. They also allow the manufacture of new forms and customized versions of medical/surgical tools. For example, implants for orthopedic and craniofacial surgery, and custom-made hearing aid ear-canal fitments.
- Allows for the precise fabrication of drug delivery systems with exact controlled release profiles and tailored properties. These systems deliver improved efficacy, safety, and patient compliance with medications.
- These technologies are being increasingly used to produce surgical instruments, guides, and implants with complex biocompatibilities and customized features. These instruments enhance surgical precision, minimize tissue trauma, and greatly advance minimally invasive procedures.
What Role Does 3D Printing Play in the Aerospace Industry?
3D printing plays an increasingly crucial role in the aerospace design, manufacture, and operations areas. It enhances design flexibility, enables retained-strength lightweighting of components, and delivers rapid prototyping for design evaluation.
3D printing enables the production of otherwise non-manufacturable or uneconomically complex geometries and intricate components. It helps in the fabrication of lightweight structures with optimized functional geometries while minimizing material usage. 3D printing also accelerates the prototyping and iteration process in aerospace by providing increasingly functional prototypes. Aerospace manufacturers can exploit up-to-date 3D printing to rapidly acquire customized components tailored to specific aircraft configurations, mission requirements, or customer preferences.
To learn more, see our article on 3D Printing in Aerospace.
How Are Large-Scale 3D Printing Applications in Construction Being Explored?
Various research organizations and companies are experimenting with 3D printing to fabricate building components such as: walls, floors, columns, and facades in centralized facilities rather than on-site. Large-format 3D printers can apply construction materials, such as: concrete, cementitious compounds, or polymer composites by similar methods to small-scale fused filament fabrication (FFF) polymer printers. Large-format printing is also being used to construct entire architectural structures such as: houses, pavilions, and bridges. These printers can create monolithic structures with reduced material waste and shortened construction time compared to traditional building methods. Large-format 3D printing can equip architects and builders with greater freedom to deliver more-complex designs and less-conventional building shapes that would otherwise be challenging or impractical, without greatly increasing costs.
Mobile/portable large-format 3D printers are under development for on-site construction applications. On-site 3D printing reduces transportation costs, logistics challenges, and construction time, which can be particularly useful in remote or inaccessible locations. Such printers have the potential to address short-term housing shortages and provide rapid shelter solutions in emergencies or disaster areas.
What Changes Are 3D Printing Making in Manufacturing, Especially for Complex, Customized Parts?
3D printing delivers design freedom that equips designers and engineers to deliver highly complex and intricate geometries that are otherwise impractical to achieve by traditional manufacturing methods. This design freedom allows for aggressive optimization of part performance, functionality, and aesthetics and lower accommodation of the restrictions of manufacturing processes. Digital fabrication of parts on-demand, direct from 3D-file design data is allowing manufacturers to offer personalized products to customers. This is currently focused on medical implants, prostheses, and orthotics, but the effect on consumer goods demanding unique features or branding is beginning to be felt.
3D printing enables rapid prototyping and iteration cycles, reducing design-cycle delays in product development, design evaluation, and manufacture. With the advanced use of 3D printing technologies, manufacturers can deliver parts on-demand at the point of use. This reduces inventory, transportation costs, and lead times otherwise associated with traditional manufacturing/distribution.
Does 3D Printing Integrate With AI and Robotics To Improve Efficiency and Capabilities?
Yes, 3D printing integrates exceptionally well with AI (Artificial Intelligence), Industry 4.0, and robotics to deliver improved efficiency and higher operational capabilities in manufacturing and other industries.
AI algorithms process big data about operations and can perform multi-stage generative design simulations. They optimize the design of 3D-printed parts for specific performance criteria, such as: weight reduction, structural integrity, or thermal management.
Industry 4.0 concepts such as cyber-physical systems (CPS) and the Industrial Internet of Things (IIoT) equip the integration of 3D printing and robotics into autonomous manufacturing systems. Robots equipped with AI-driven controllers and sensors can perform deviation-prone tasks such as: part handling, post-processing, and assembly. This increases the overall process efficiency and flexibility.
Robotic systems equipped with 3D printing extrusion heads or plastic/metal powder/metal wire deposition devices can perform additive manufacturing tasks autonomously. Robotic movements can be monitored for print quality and adjusted in real time. This enables continuous production and adaptive/self-healing manufacturing strategies.
Summary
This article presented the possible future of 3D printing, explained it, and discussed each possibility in detail. To learn more about 3D printing, contact a Xometry representative.
Xometry provides a wide range of manufacturing capabilities, including 3D printing and other value-added services for all of your prototyping and production needs. Visit our website to learn more or to request a free, no-obligation quote.
Copyright and Trademark Notices
- FDM® is a registered trademark of Stratasys Inc.
- Ultem® is a registered trademark of SABIC Innovative Plastics IP BV (formerly GE Plastics)
Disclaimer
The content appearing on this webpage is for informational purposes only. Xometry makes no representation or warranty of any kind, be it expressed or implied, as to the accuracy, completeness, or validity of the information. Any performance parameters, geometric tolerances, specific design features, quality and types of materials, or processes should not be inferred to represent what will be delivered by third-party suppliers or manufacturers through Xometry’s network. Buyers seeking quotes for parts are responsible for defining the specific requirements for those parts. Please refer to our terms and conditions for more information.
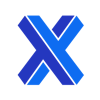